
🌱 Rhubarbs key to recycling electric car batteries
Researchers at Chalmers University of Technology have devised a new and efficient way to recycle metals from electric car batteries. The method enables the recycling of 100 percent of aluminum and 98 percent of lithium from used electric car batteries.
Share this story!
- Researchers at Chalmers University of Technology have devised a new and efficient way to recycle metals from electric car batteries.
- The method enables the recycling of 100 percent of aluminum and 98 percent of lithium from used electric car batteries.
- No expensive or harmful chemicals are required in the process; instead, oxalic acid, which is found in rhubarb among other things, is used.
At Chalmers University of Technology's battery recycling lab, Léa Rouquette and research leader Martina Petranikova demonstrate how the new method works. The lab houses spent automotive battery cells, and their crushed contents, in the form of a finely ground black powder, are dissolved in a clear liquid, oxalic acid. It's an environmentally friendly ingredient also found in plants like rhubarb and spinach.
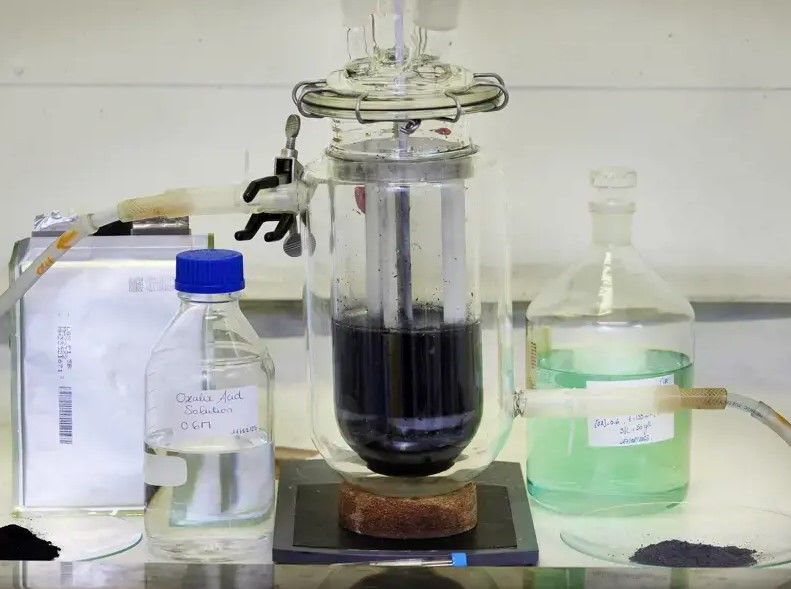
Léa Rouquette mixes the liquid and powder in something resembling a kitchen blender. Although it looks easy, almost as if she were making coffee, the exact approach is unique and a recently published scientific breakthrough. By fine-tuning the temperature, concentration, and time, the researchers have developed a new recipe for using oxalic acid.
"So far, no one has managed to find the exact right conditions to separate this much lithium with oxalic acid, and also remove all the aluminum at the same time, says Léa Rouquette", a doctoral student at the Department of Chemistry and Chemical Engineering at Chalmers.
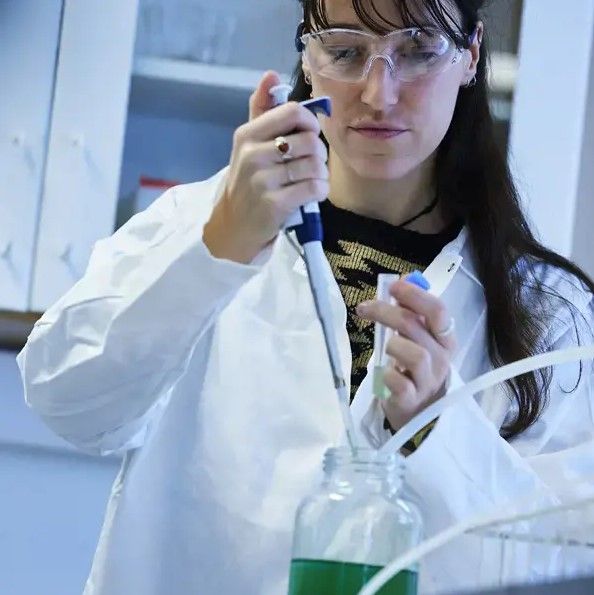
Reversed order compared to other methods
The liquid-based recycling method is referred to as hydrometallurgy. In traditional hydrometallurgy, the "impurities" in the material such as aluminum and copper are removed first, and then valuable metals like lithium, cobalt, nickel, and manganese can be recovered.
Even though only small amounts of aluminum and copper remain, several purification steps are required, and each step in the process causes waste. In the new method, researchers flip the script and separate lithium first along with aluminum. This way, they can reduce the waste of valuable metals needed to manufacture new batteries.
"Alternatives to today's inorganic chemicals are needed. Additionally, one of the biggest bottlenecks in today's processes is removing residual materials like aluminum. This is an innovative method that can provide the recycling industry with new alternatives and help solve problems that hinder development, says Martina Petranikova," associate professor at the Department of Chemistry and Chemical Engineering at Chalmers.
By becoming a premium supporter, you help in the creation and sharing of fact-based optimistic news all over the world.